Are you looking for an article that has everything about injection moulding? If yes, then finally your search is over. There is no doubt in saying injection moulding is a popular manufacturing process and it is used all over the place. The best thing about this process is that it is very interesting and used to make a lot of useful products. So if you are curious to know more, then this article is very beneficial for you. In this article, you will get all the information about injection moulding and most of the frequently asked questions related to it will also be answered. So if this sounds compelling, then keep reading this article.
What is Injection Moulding?
Injection Moulding is generally a manufacturing process that is used for making various items such as trinkets, plastic toys, cellphones, auto parts, etc. In simple words, most of the products that you use in your daily lives are made through an injection moulding process. Several processes are involved in this and thermoplastic and thermoset are materials that are used in it. Generally, the materials are heated, melted and thrown into the cold cavity. After the material gets cooled down, the ejection process takes place.
Though injection moulding is a common process and most companies use this. But not every company provides genuine quality, so if you have any plastic mold request, then LOXIN mold company (https://www.loxinmold.com/) is the best option for you. They have been in the business for a long time and provides amazing service.
Injection Moulding Process
So after discussing the fundamental information regarding injection moulding, it’s time to talk about the entire process in a detailed manner.
The mold that is used in the process comprise of two halves. With the help of a hydraulic machine the halves are clamped in this process, then one half is connected to the injection moulding machine. When the material injection takes place, the clamping unit pushes the mold halves and put enough force, helps in secure them. The clamping force needed is associated to the resin property, along with the injection pressure needed to complete or fill up the cavity.
2- Injection
Under the mixture of heat and pressure, the resin in the injection barrel liquefies. The barrel provides heat bands that help in increasing the correct melting points temperature. The main feature of this process is the accurate temperature. When the temperature get too high, the shear stress, and fill speed is affected, resulting in bad product quality.
If the temperature is too low, liquefaction of the resin will not be proper. The screw inside the injection barrel throws the molten material, after the resin is liquefied, the mold cavity is filled. This stage success depends on sink mark displacement and packing, fill speed, and shear stress.
3- Cooling
When the liquefied plastic comes in contact with inner mold surfaces, it cools down. As the plastic cools, it starts forming the shape of the desired part. Some shrinkage can also occur during cooling. Proper packing in the injection phase reduces the material shrinkage. Until the needed cooling time has progresses, the mold is kept closed. The cooling period is determined from the wall parts thickness resin’s thermodynamic properties.
4- Ejection
Once the molded part completely solidifies, it gets ejected. In the cooling time, maximum force is put in to the ejected part. This prevents it from sticking to the mold because of shrinkage. To make the smooth release possible, mold cavity surface is sprayed by a mold release agent, before the material injection. After ejecting, the next shot the mold is clamped until the next shot.
Plastic Moulding Supplies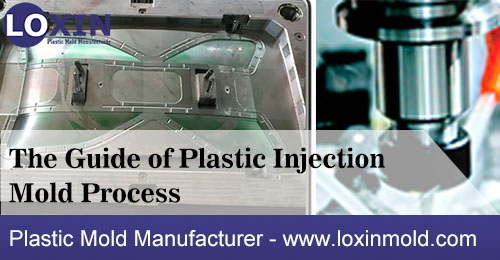
As mentioned above that injection moulding is an interesting method of fabricating plastic parts. To execute this process, plastic moulding supplies such as plastic injection mold are needed and it very important to select them properly. So here is a list of the most common supplies required for plastic moulding.
• Polypropylene (PP)
• Acrylonitrile Butadiene Styrene (ABS)
• Polyamide (Nylon)
• High-Density Polyethylene (HDPE)
• Polycarbonate (PC)
• ABS + PC Blend (used for electronics)
Conclusion
Injecting moulding has been in the industry for some time and it has made the work very easy. Another great thing about this technology is that it provides great results on a massive scale. Along with this, it is also a very useful option for final prototypes used product and consumer testing. Despite being so popular, it very flexible and affordable for early-stage product designing. Hope this article will solve some of your doubts and queries and give you some helpful information.