How Dose Plastic Injection Moulding Process Steps From China
Most of the plastic products as well as the products having plastic parts we use in our day-to-day life, in our home or office, are made through an injection molding process.
These items may include storage bins, food containers, toys, bags, kitchen items, utensils, devices, stationery, and gadgets, etc. In other words, during last few decades plastic has gained enormous popularity all over the world for manufacturing a wide variety of products as it can be molded into any kind of shape with the help of injection molding process.
The process of plastic injection molding in China gained popularity throughout the world because of the low cost of developing molding designs and producing plastic prototypes.
A Chinese plastic mold company can create prototype molds at a very reasonable cost by using heated molten plastic in the injection molding process.
Steps of plastic injection molding process in China
In China, manufacturing in the plastic industry is done through the machines of injection molding which allow a mold company to produce plastic products in large qualities as soon as possible. These machines use the same mold again and again to produce the products of the same kind which may not be possible while molding every piece by hand.
Though the process of injection molding f plastic looks easy and simple but it involves several steps to produce a quality product. The steps in the plastic injection molding process include:
Mold designing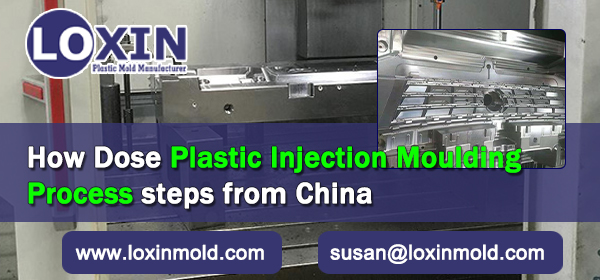
The first step of the injection molding process is to create a molding design to create a final product of your dreams. You will have to use a lot of skills and time to create the design of the mold. Various types of mold designs are created by engineers by using a computer. In these designs, they include every detail of the product you want to manufacture to sell it in the market including logos, patterns, gripping surface, variety of finish, layers of texture and graphics, etc.
They use a machine to carve the final design of the mold exactly as per the dimensions of the end product. In order to make these molds long-lasting and durable, they use steel to manufacture them otherwise their repeated use can affect the quality of final products. While creating a mold, the engineers in a mold company should ensure that any defect can be prevented in the final product by making the transition right with the help of space provided in the mold.
They can easily judge the exact shape and size of the mold by making its digital model. While creating a mold design the engineers will have to be very precise as you will have to recall your product if its mold has even a minor defect. When mold is finally designed then you will have to choose the type of plastic you will want to use to create final products.
Selection of right material
The manufacturers of plastic products will have to choose the right type of plastic to be used in injection molding machines. At present various types of plastic is used in China to manufacture various types of plastic prototypes as well as final products depending upon the quality of the product they want to produce.
In order to mix various types of raw materials in the right proportion injection molding companies in China engage chemical engineers. It allows them to choose the best combination for their prototype molds by combining various types of polymers in different proportions. In other words, it can be said that every plastic cannot be suitable for producing any type of plastic product. You can produce the right product through an injection molding machine by using the right type of materials.
Testing of prototype
The plastic prototypes created by using the right materials have to be tested before producing the final products in large quantities to ensure its proper working of the design as well as the mixture used to produce it. Actually, prototype molds are created to ensure the shape and usability of the final product so that it can be adjusted as required before starting to produce the final product.
Checking the maintenance and running order of the parts of the injection molding machine is also a standard procedure to be followed before starting the production of the final product. It can help in avoiding mishaps and accidents as well as ensuring the quality of the product during the final manufacturing process.
Start manufacturing
The process of manufacturing the final product starts by using the prototype molds in the machines used for plastic injection molding in China. You will have to feed plastic pellets into the machine to start manufacturing the final product in large quantities. The pallets can be fed into the heater to melt it manually or automatically according to the type of your machine. While heating the plastic raw materials high pressure and friction are used most of the time.
The liquid molten plastic is injected into the molds through a nozzle to allow it to enter into the cavity of the mold. Then the molten plastic is allowed to harden by cooling down in the mold. When the plastic becomes hard then the mold, closed with the help of steel clamps known as platens, is opened into pieces to take out the final product. In this way, you can manufacture the desired number of pieces of the final product of the same quality by using this method repeatedly.
Introduction of a Chinese plastic injection molding company
LOXIN Mold Company is one of the leading plastic injection molding companies in China that provide manufacturing services of high-quality prototype molds to their clients throughout the world including the USA and European countries. This mold company is famous among its customers due to the best quality of its molding designs.
They keep the satisfaction of their customers at priority. They assure to provide high-quality plastic prototypes at very reasonable prices by focusing on lean manufacturing process along with using the best quality management system of ISO9001:2008.
In this way, Loxin Mold Company provides quality molds as per the demand of its customers with the help of its quality control staff and management team. They take care of the compliance of the specification, implement the improvements in the manufacturing practices to produce the best products to their customers.